Projektowanie
Proces produkcji w firmie Metalpol rozpoczyna się już na etapie zaprojektowania wyrobu. Robi się to na podstawie dostarczonego przez klienta rysunku technicznego wraz ze specyfikacją i wymaganiami określonymi zapytaniem ofertowym. Do zaprojektowania wyrobu, specjaliści Działu Technologicznego wykorzystują komputerowe systemy wspomagania projektowania typu CAD – Autodesk Inventor oraz CAM – hyperMILL firmy OPEN MIND
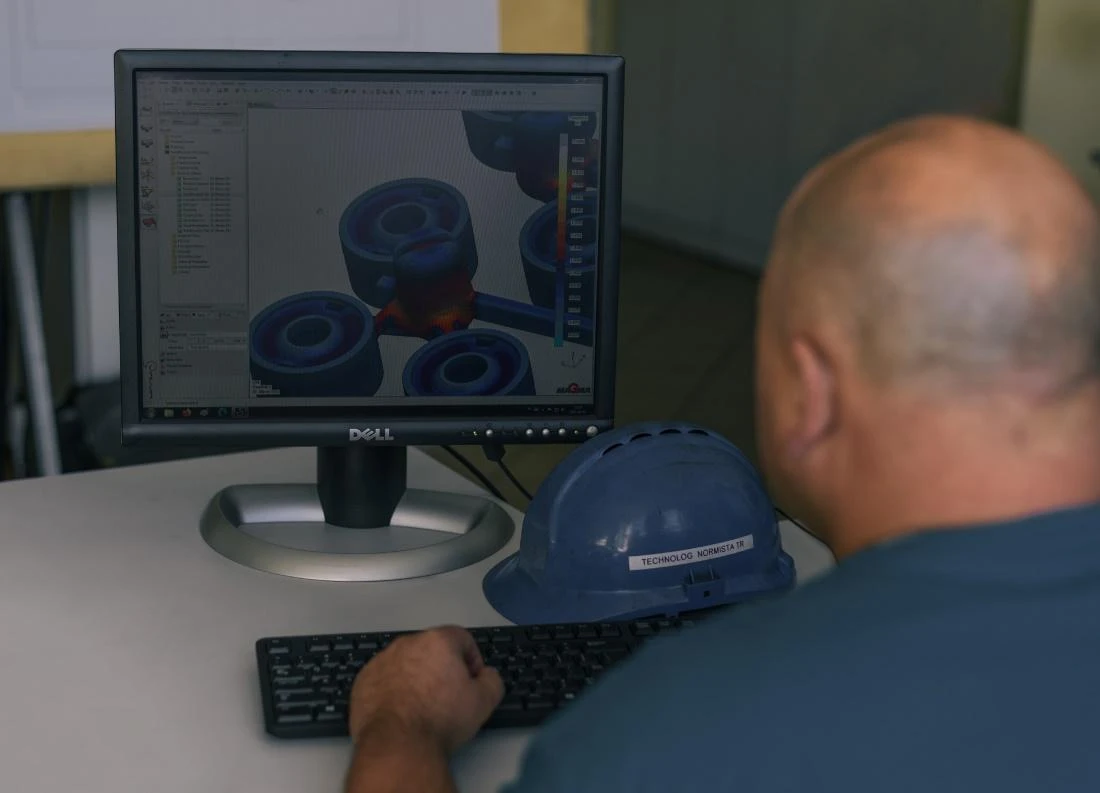
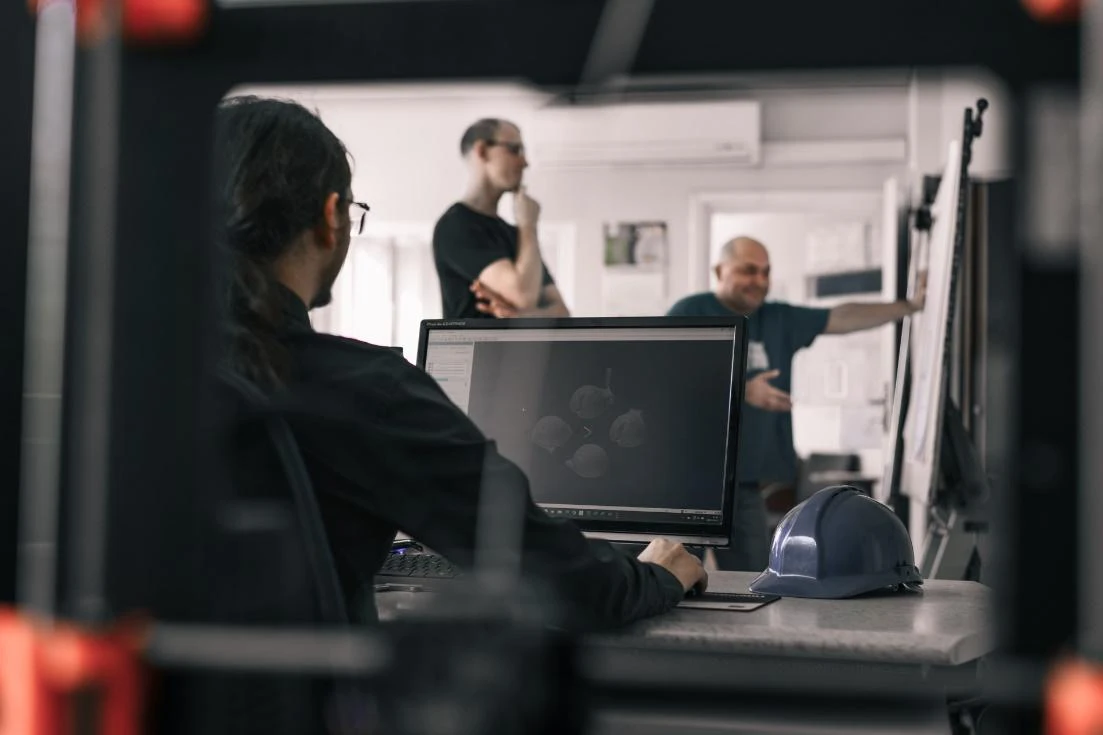
Do analizy procesu zalewania, optymalizacji układów wlewowych, rozkładu temperatur oraz przewidywania własności mechanicznych odlewu wykorzystywany jest w firmie Metalpol program MAGMASOFT.
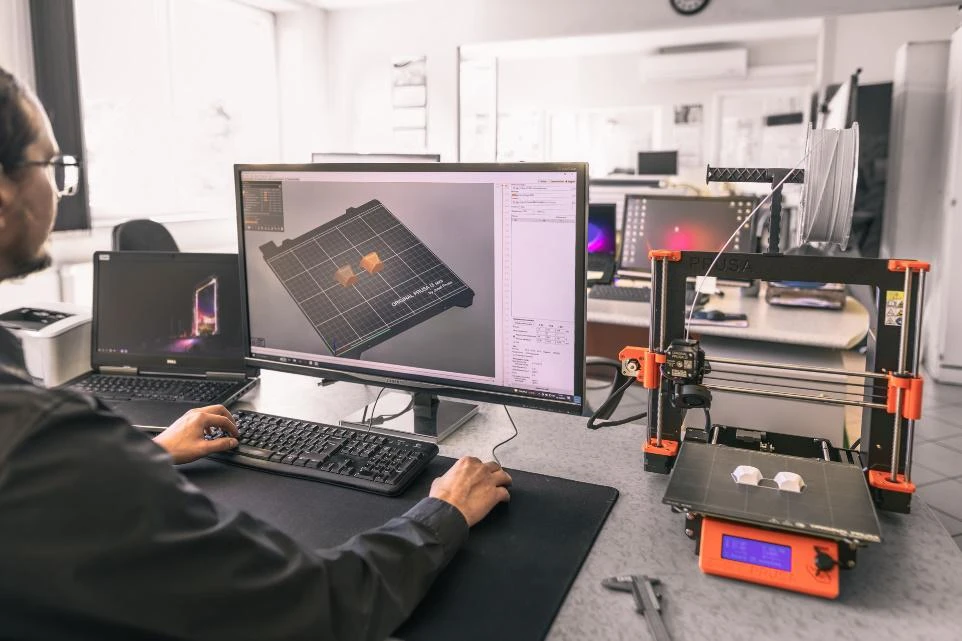
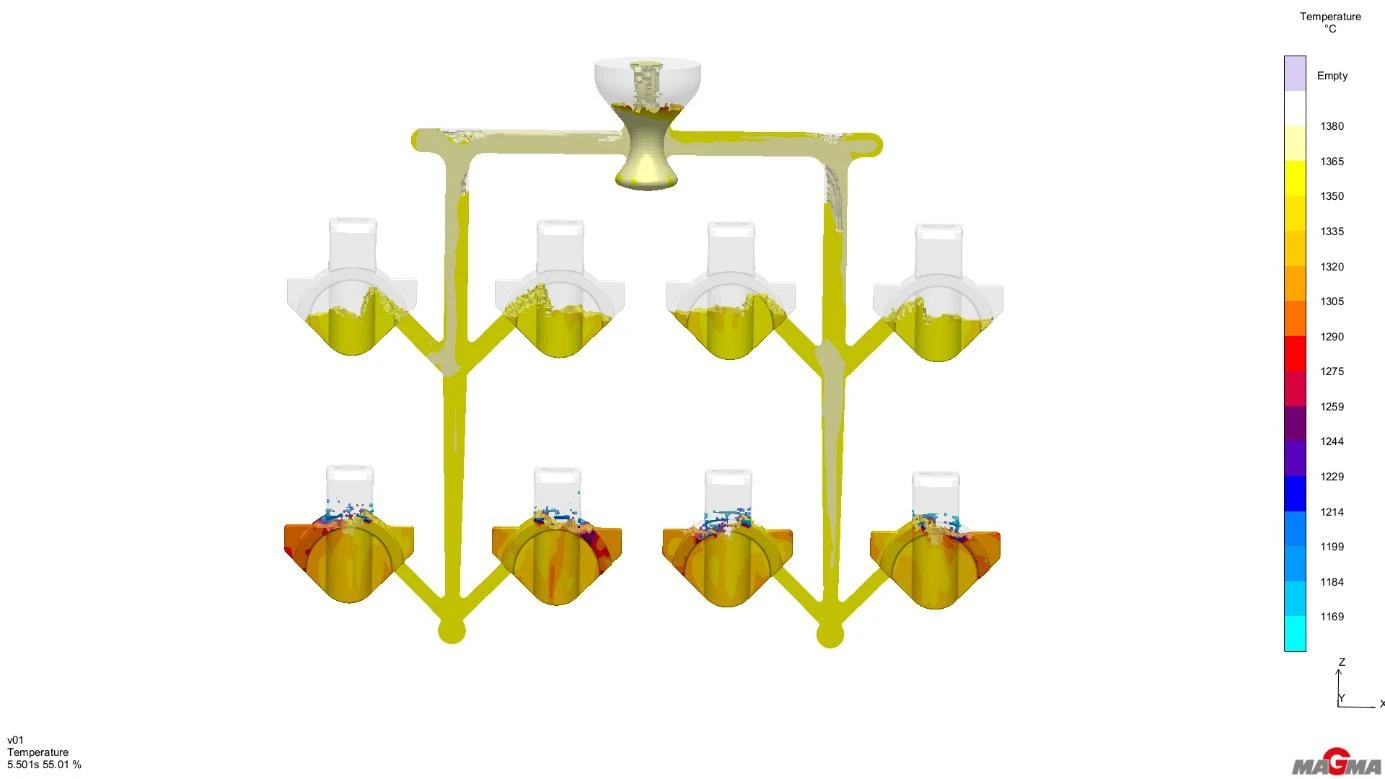
Systemy wspomagania komputerowego znacznie przyśpieszają czas projektowania i przygotowania odlewu do produkcji. Umożliwiają współpracę z klientem na poziomie projektowania wyrobu, co w efekcie prowadzi do optymalizacji kosztów wytwarzania, poprawy właściwości użytkowych oraz zmaksymalizowania jakości wyrobu.
Modelarnia
Wydział ten wykonuje większość oprzyrządowań służących do produkcji odlewów. Jest on wyposażony w dwa centra obróbcze: MIKRON VCE 1000 i HASS VF-8 oraz tradycyjny park maszynowy. W zależności od wielkości serii i stopnia skomplikowania odlewu, oprzyrządowanie i narzędzia odlewnicze są wykonywane z materiałów takich jak aluminium i różne stopy metali, które charakteryzują się wysoką wytrzymałością oraz odpornością na obciążenia termiczne. Wydział zajmuje się zarówno produkcją nowych modeli i rdzennic, jak i regeneracją oraz utrzymaniem w dobrym stanie wszystkich używanych modeli, rdzennic oraz oprzyrządowania obróbczego, które służą do produkcji detali. Dzięki temu zapewniona jest ich trwałość oraz niezawodność w procesie produkcyjnym
Topialnia
Metal dostarczany jest na linie odlewnicze przez topialnię wyposażoną w cztery 6-cio tonowe piece indukcyjne średniej częstotliwości - dwa produkcji firmy JUNKER i dwa firmy ABB. Kluczowym elementem procesu technologicznego jest sferoidyzacja płynnego metalu. Jest ona przeprowadzana w smukłych kadziach syfonowych przy użyciu metody drutowej, pilotowanej komputerowo, gwarantującej powtarzalność oraz stabilność procesu.
ŻELIWO SFEROIDALNE (WG. PN-EN 1563) | Żeliwo szare (wg. PN-EN 1561) |
---|---|
EN - GJS - 400 - 15 | EN - GJL - 200 |
EN - GJS - 400 - 18 | EN - GJL - 250 |
EN - GJS - 400 - 18LT | EN - GJL - 300 |
EN - GJS - 450 - 10 | EN - GJL - HB175 |
EN - GJS - 500 - 7 |
EN - GJL - HB195 |
EN - GJS - 600 - 3 | |
EN - GJS - 400 - 2 |
Formiernia
Firma Metalpol posiada dwie, niezależne linie formierskie: LORAMENDI (rok produkcji 2017) oraz linię BMD.
Automatyczna Linia formierska LORAMENDI e-VMM 6080B, z pionowym podziałem formy, z napędem elektrycznym o wielkości płyt 600 x 775 x 150 do 500 mm i wydajności 450 form na godzinę bez rdzeni i 400 form/godzinę z rdzeniami o wadze odlewów 0,2 – 30kg.
Linia posiada zmienną komorę formowania o wymiarze większej formy 650 x 850 x 150 do 500 mm.
W linii zastosowano:
- precyzyjny przenośnik form PMC o długości 22m,
- zsynchronizowany przenośnik SBC o długości 76m,
- urządzenie do zakładania rdzeni CS z kurtyna świetlną,
- urządzenie do szybkiej wymiany płyt modelowych QPC
- napęd elektryczny
- zsynchronizowaną współpracę z zalewarką i Stacją przerobu Mas Formierskich
Zalewanie form i modyfikacja żeliwa odbywa się przy użyciu elektrycznego bez induktorowego pieca zalewowego firmy CIME CRESCENZI CAP wyposażonego w:
- optyczny system kontroli procesu zalewania form
- samouczący się system automatycznego zalewania form
- laserowy system naprowadzania zatyczki
- system modyfikacji na strugę żeliwa
- ciągły pomiar temperatury żeliwa w procesie zalewania.
Linia formierska z poziomym podziałem formy produkcji firmy BMD używa skrzynek o wymiarach 750 x 850 x 2 x 250 mm. Zalewanie form odbywa się ze specjalnych kadzi syfonowych za pomocą zalewarki, która przemieszcza się wzdłuż pierwszego magazynu form. W zależności od gabarytów i wagi produktów, roczne zdolności produkcyjne linii BMD wynoszą ok. 10.000 do 15.000 ton.
Przerób masy formierskiej
Mieszarka intensywnego mieszania P/3500H2
Jest to mieszarka włoskiej firmy Belloi Romagnioli o pojemności do 4 500 kg, wydajności 120 ton masy/godzinę
Producent
Mieszarka wyposażona jest w:
- hydrauliczny napęd mieszadeł
- automatyczne laboratorium GSC do pomiaru parametrów masy formierskiej
- automatyczny system naważania masy formierskiej
- ceramiczne wyłożenie dna i ścian bocznych mieszarki
- automatyczny układ dozowania wody, mieszanki bentonitu i nośnika węgla, oraz świeżego piasku
Chłodziarka masy formierskiej
Eirich – Niemcy typ CM4:
- wydajność chłodziarki 120 t/h
- temperatura masy po schłodzeniu 40 stopni Celsjusza
- wilgotność masy 1,8 – 2,2 %
- ósemkowy system mieszania wewnątrz chłodziarki
Rdzeniarnia
Produkcja rdzeni odbywa się w technologii zimnej i gorącej rdzennicy na następujących maszynach:
Technologia | Model | Pojemność | Podział | Ilość |
---|---|---|---|---|
Zimna | AHB | 30L | Poz. I Pion. |
1 |
Zimna | SODIM | 12L | Poz. I Pion. |
1 |
Zimna | ROEPERWERK | 16L | Pionowy | 2 |
Zimna | PRIMAFOND | 12L | Pionowy | 1 |
Gorąca | U-200 / U-250 | - | Pionowy | 5 |
Gorąca | FM | - | Pionowy | 1 |
Gorąca | PSI | - | Pionowy | 4 |
Rdzeniarnia dysponuje również stacją z mieszalnikami do pokryć rdzeni, indywidualnymi mobilnymi stanowiskami do pokrywania rdzeni powłokami oraz suszarnią.
Oczyszczalnia
Układy wlewowe i zasilacze oddzielane są od odlewów przy pomocy klinów hydraulicznych oraz obcinarek tarczowych. Śrutowanie odlewów realizowane jest za pomocą śruciarek komorowych GOWG-08, EURO-80, OWT-400 oraz śruciarki zawieszkowej firmy STEM-CH22/3W2C i przelotowej SISSON LEHMANN.
Do wykańczania odlewów, tak z linii LORAMENDI, jak i BMD, stosowane są zespoły szlifierek dwutarczowych oraz stanowiska do wykańczania odlewów. Szlifowanie i wykańczanie wyrobów wymagających wysokiej precyzji oraz powtarzalności realizowane jest na maszynach CNC marki KOYAMA oraz SIIF.
Obróbka i malowanie
Wydział ten dysponuje szeregiem maszyn umożliwiających obróbkę odlewów produkowanych przez odlewnie:
- 4 centra poziome CNC 4 - osiowe
- 4 tokarki CNC, w tym 1 tokarka 2- wrzecionowa z manipulatorem
- obrabiarki zespołowe przystosowane do obróbki elementów składowych armatury
- tradycyjny park maszynowy typu tokarki, wiertarki, wytaczarki.
Na wydziale obróbki mechanicznej znajdują się również stanowiska montażu armatury przemysłowej produkowanej przez METALPOL oraz stanowiska probiercze do przeprowadzania prób ciśnieniowych, kształtek i hydrantów.
Firma prowadzi również aktywną współpracę ze swoimi klientami w zakresie:
- obróbki mechanicznej odlewów na maszynach typu CNC
- malowania odlewów wg wymagań i specyfikacji Klientów:
- kataforetycznie
- zanurzeniowo
- natryskowo
- proszkowo
Kontrola jakości
METALPOL od 2000 roku posiada certyfikat jakości ISO 9001:2008, ISO TS 16949:2008 oraz ISO 14001:2004. Zadaniem Działu Jakości jest prowadzenie procesu kontroli produkcji przy wykorzystaniu specjalistycznego sprzętu pozwalającego na prowadzenie niezbędnych badań procesu i wyrobu a w szczególności:
- badania parametrów mas formierskich: przepuszczalność, wytrzymałość, zagęszczalność, wilgotność, wilgotność, zawartość lepiszcza, zawartość gliny aktywnej,
- analiza składu chemicznego odlewów i materiałów wsadowych na spektrometrze emisyjnym i cyfrowym,
- badania wytrzymałościowe (Rm, Re, A5, HB, KCU, KCV),
- badania mikrostruktur metalu,
- badania wymiarowe na maszynie pomiarowej 3D MITUTOYO,
- pomiar kształtu odlewu exiXscan 3D – przy pomocy specjalisztycznego oprogramowania uzyskując parametryczne formaty CAD, gotowe do dalszego modelowania i oceny.
Wszystkie certyfikaty i dopuszczenia są do pobrania z naszej strony internetowej: www. metalpol.com